If you want to hop on the Industry 4.0 train, it is important to have a very small use case in mind. Our three-step approach is simple: make sure to narrow down your use case, engineer the system and data, and keep factory operationalization in mind when designing your solution.
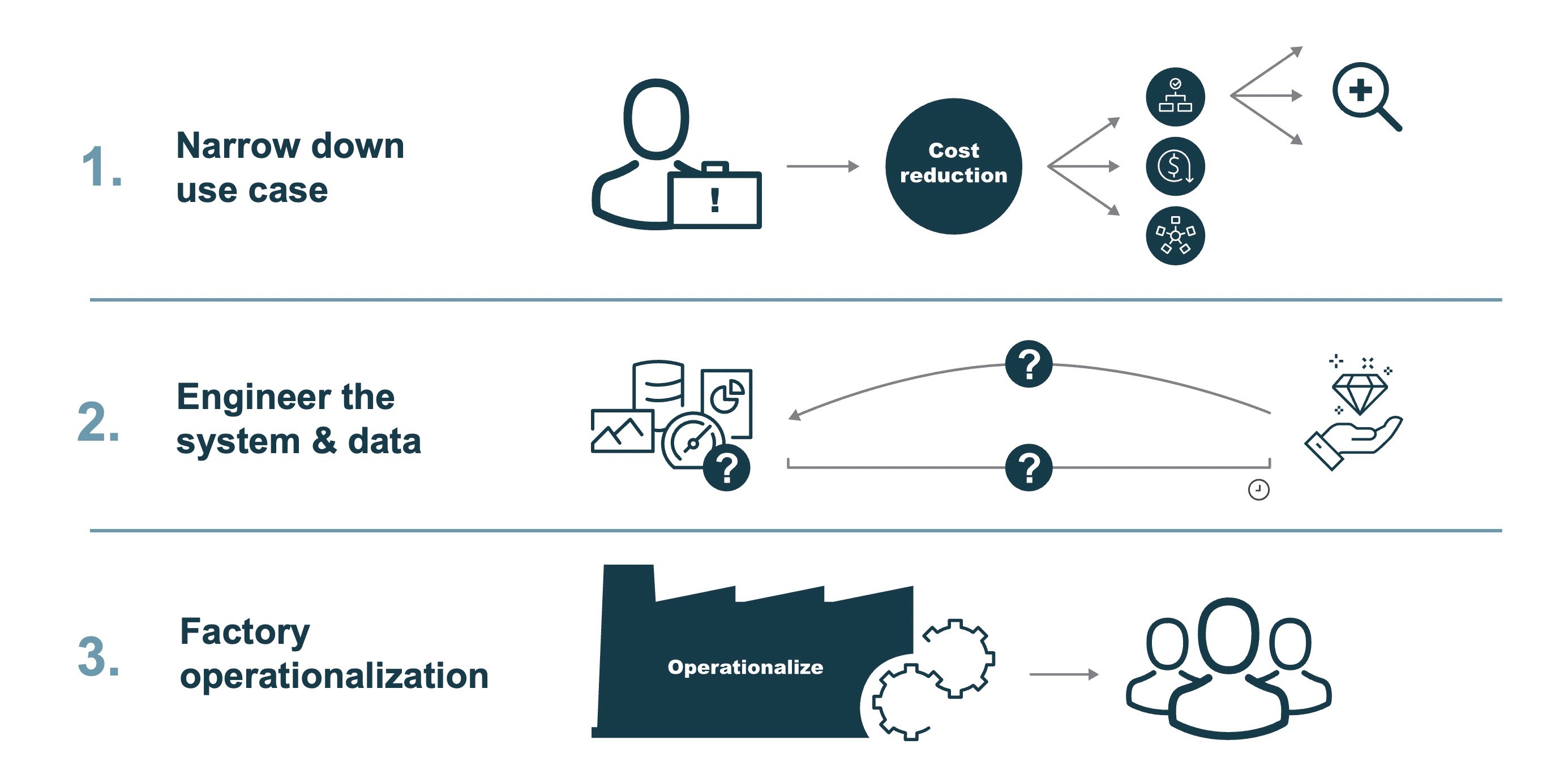
We sat down with our customer AMF to explore the business challenges they were encountering. Together, we searched for a solution on how to reduce costs in the production process, and narrowed it down to a small use case. It turned out that cheese is the most expensive ingredient on a pizza. In the production process, 10-inch pizzas are supposed to have exactly 65 grams of cheese with a margin of only plus or minus 2%. So we narrowed down the broad goal of ‘increasing efficiency and cost by using AI and automation’ to the small use case of staying within that 2% margin by using vision technology. (Why vision instead of a simple measuring sensor? Those are too fragile for a moist factory environment with moving belts).
The next step was to engineer the system. On paper, the system looks simple: pizza bases with sauce go in, a cheese applicator deposits the cheese, and pizzas with cheese come out. So, by simply adding a camera to the production line to visually measure the amount of cheese, we can achieve our goal. In practice, however, it turned out to be a bit more complicated.
For example, the camera needs to know when a pizza passes by on the conveyor belt, so it has to be triggered by a motion sensor. The camera also needs to be placed high enough to not be damaged when the production line is cleaned with hot water. In that case, a suitable lighting system is required to ensure good quality images. Those images then have to be sent to a database where an algorithm will translate each image into weight. In a factory environment with poor internet connection, the cloud is not a viable option. That is why we chose to add an edge computer into the mix.
Challenges will arise every step of the way. The key here is not trying to solve everything at the same time but to keep taking small steps forward toward the end goal. In this case, the final setup consisted of a camera, a motion sensor, a light bar, an edge computer, a cloud data lake, a labeling app, a dashboard, and a PLC adjustment. The last piece of the puzzle is change management — designed with operations in the back of your mind. For this use case, this meant delivering an application for operators to agree or disagree with the algorithm’s advice to adjust the belt speed. This served as an in-between step before trusting the system well enough to fully automate the way of working.
The moral of the story is: ‘solving world hunger’ is a big challenge. Make sure you think big, but design small, and focus on a marketable viable product.
Interview Marianne Faro for the BIC fieldlab Technology Update (Dutch only):